 Книжкові видання та компакт-диски  Журнали та продовжувані видання  Автореферати дисертацій  Реферативна база даних  Наукова періодика України  Тематичний навігатор  Авторитетний файл імен осіб
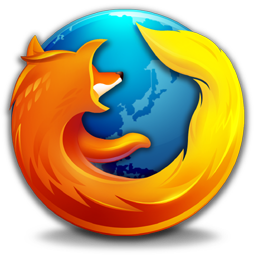 |
Для швидкої роботи та реалізації всіх функціональних можливостей пошукової системи використовуйте браузер "Mozilla Firefox" |
|
|
Повнотекстовий пошук
Пошуковий запит: (<.>A=Gurey V$<.>) |
Загальна кількість знайдених документів : 8
Представлено документи з 1 до 8
|
1. |
Hurey I. Simulation model of dynamic processes during friction hardening of the flat surfaces [Електронний ресурс] / I. Hurey, V. Gurey, P. Dmyterko // Вісник Національного університету "Львівська політехніка". Оптимізація виробничих процесів і технічний контроль у машинобудуванні та приладобудуванні. - 2013. - № 772. - С. 80-85. - Режим доступу: http://nbuv.gov.ua/UJRN/VNULPO_2013_772_16 Розроблено імітаційну модель динамічних процесів під час фрикційного зміцнення плоских поверхонь деталей машин.
| 2. |
Gurey V. Machematical model of dynamic processes during friction hardening of flat surfaces [Електронний ресурс] / V. Gurey, V. Korendiy, P. Dmyterko // Вісник Національного університету "Львівська політехніка". Динаміка, міцність та проектування машин і приладів. - 2014. - № 788. - С. 79-85. - Режим доступу: http://nbuv.gov.ua/UJRN/VNULPDM_2014_788_15
| 3. |
Dmyterko P. Research of Influence of Oscillations of Tool-Part System on Roughness of Surface Layer during High-Speed Friction Strengthening [Електронний ресурс] / P. Dmyterko, Y. Novitskyi, V. Gurey // Ukrainian journal of mechanical engineering and materials science. - 2016. - Vol. 2, Num. 1. - С. 47-54. - Режим доступу: http://nbuv.gov.ua/UJRN/ujmems_2016_2_1_7 During the discontinued friction strengthening except of the high-speed friction the processes of high-frequency shock loadings appears in the tool-part contact zone. The vibrations occur in the machine elastic system. During the vibrations of elastic systems, in the material of elastic elements and in the connecting units of the structure parts the energy dissipation into the ambient medium takes place. The energy dissipation of vibrations occurs due to the influence of the inelastic resistance forces on which the energy of the oscillatory system is spent. The vibrations of the tool-part system during the friction strengthening are similar to forced oscillations. However, for some particles of the part these oscillations are damped ones because the tool moves along the surface. The vibrations of the elastic system of the machine during the discontinued friction strengthening in the first approximation may be considered as free oscillations. For their investigation let us use the method of shock (impact) perturbation with a help of special measuring hammer which allows defining of the damping coefficient. With a help of the accelerometer and the hammer the shock (impact) curve and the registration curve of the tool-part vibrations were obtained. The obtained registration curve of tool-part vibrations was expanded into the Fourier series and with a help of MatLab program the obtained signal was filtered. Due to determination of the amplitude of vibrations and the oscillation period the logarithmic decrement of damping was defined. This parameter may be used for determination of the dynamic parameters of the oscillatory system of the converted machine. For defining the oscillations which arises in the part being machined we used the dynamometer, in which the piezo-crystal sensor was rigidly fixed. This sensor allows the readout of oscillations along three directions (along vertical, horizontal and transversal axis). Experimental research showed that the amplitude increased with increasing the number of processing modes and the oscillation character has exact wave-like form. The working process along the longitudinal direction has step-wise character. The single contact zone is heated to high temperatures; the metal softens; the friction coefficient decreases and the step-wise transportation of the part along the longitudal direction is being carried out. These phenomena are also confirmed by the figure of the machined surface and by the results of investigation of the topography of the machined surface. It is also experimentally determined that horizontal and vertical displacements of the spindle and the table vibrate with the frequencies close to resonance ones. With increasing of the tool rotation speed these vibrations have the character of damped ones and this phenomenon allows reducing the parameters of roughness, undulation and flatness of the surfaces being strengthened.
| 4. |
Hurey I. Formation of residual stresses during discontinuous friction treatment [Електронний ресурс] / I. Hurey, V. Gurey, M. Bartoszuk, T. Hurey // Journal of engineering sciences. - 2021. - Vol. 8, Iss. 1. - С. C38-C44. - Режим доступу: http://nbuv.gov.ua/UJRN/jes_2021_8_1_7 The tool with grooves on its working surface is used to improve the properties of the strengthened layer. This allows us to reduce the structure's grain size and increase the thickness of the layer and its hardness. Mineral oil and mineral oil with active additives containing polymers are used as a technological medium during friction treatment. It is shown that the technological medium used during the friction treatment affects the nature of the residual stresses' distribution. Thus, when using mineral oil with active additives containing polymers, residual compressive stresses are more significant in magnitude and depth than when treating mineral oil. The nature of the residual stresses diagram depends on the treated surface' shape. After friction treatment of cylindrical surfaces, the highest compressive stresses near the treated surface decreases with depth. And after friction treatment of flat surfaces near the treated surface, the compressive stresses are small. They increase with depth, pass through the maximum, and then decrease to the original values. The technological medium used during friction treatment affects residual stresses in the grains and in the crystal lattice.
| 5. |
Gurey V. Wear resistance of strengthened layers with nanocrystalline structure in friction with boundary lubrication [Електронний ресурс] / V. Gurey // Ukrainian journal of mechanical engineering and materials science. - 2020. - Vol. 6, Num. 1. - С. 83-90. - Режим доступу: http://nbuv.gov.ua/UJRN/ujmems_2020_6_1_12 Friction treatment refers to surface strengthening (hardening) methods using highly concentrated energy sources. The source of thermal energy occurs in the contact area of the tool-part due to high-speed friction (60 - 90 m/s) of the tool on the treated surface. The heating rate of the metal surface layer is 10<^>5 - 10<^>6 K/s. After moving the energy source from the contact zone, high-speed cooling of the surface layer of the metal takes place. The cooling rate is 10<^>4 - 5 x 10<^>5 K/s. Under the action of high-speed heating and cooling of the contact area of the tool-part in the surface layers, a strengthened (hardened) nanocrystalline (white) layer is formed. The formed nanocrystalline surface layer has other physical, mechanical, chemical properties in comparison with the base metal of the part. Studies have shown that in the process of friction treatment of working surfaces of parts made of Steel 40NiCr6 (quench hardening and low-tem perature tempering) a strengthened layer with a thickness of 250 - 320 <$Emu>m with a hardness of 7,6 - 9,2 GPa is formed. The grain size of the surface strengthened layer was 20 - 40 nm near the treated surface. The formation of the strengthened layer is influenced by the shape of the working surface of the tool. Thus, a strengthened layer of greater thickness and hardness is obtained when machining with a tool with transverse grooves on the working part than with a tool with a smooth working part. Experimental studies in friction with maximum lubrication of pair "Steel 40NiCr6 and Grey Cast Iron GG20" showed that the strengthened nanocrystalline layer significantly in creases the performance during sliding friction. Only samples made of steel were strengthened, counter-samples made of gray cast iron were not strengthened. The wear intensity of strengthened pair is 2,2 - 3,1 times less compared to unstrengthened pair. During the friction of the strengthened pair, the coefficient of friction and the temperature in the sliding zone also decrease. The best results were obtained when studying the friction pair in which the samples were strengthened with a tool with transverse grooves on its working part.
| 6. |
Gurey V. Simulation modelling of dynamic processes due discontinuous frictional treatment of the flat surfaces [Електронний ресурс] / V. Gurey, V. Korendiy, I. Kuzio // Ukrainian journal of mechanical engineering and materials science. - 2020. - Vol. 6, Num. 2. - С. 23-33. - Режим доступу: http://nbuv.gov.ua/UJRN/ujmems_2020_6_2_5 Abstract. Friction treatment refers to surface strengthening (hardening) methods using highly concentrated energy sources. In the course of this processing in the surface layers of the processed surfaces of parts the strengthened layer with nanocrystalline structure is formed. The formed layer has specific physical, mechanical, chemical properties, as well as improved performance properties, which are significantly different from the base metal. A highly concentrated energy source is formed in the contact area of the tool-part due to the high-speed friction (60 - 90 m/s) of the tool on the treatment surface. Frictional treatment of flat parts according to the kinematics of the process is similar to grinding. The strengthening process was carried out on an upgraded surface grinder. The tool is a metal disk made of stainless-steel. Transverse grooves are formed on the working surface of the tool to intensify the process of forming a strengthened (reinforced) layer with a nanocrystalline structure. The grooves form additional shock loads in the contact area of the tool-treatment surface of the part. These shock loads increase the shear deformation of the metal of the parts' surface during treatment, which affects into formation the quality parameters of the parts' surface and surface layer. To study the friction treatment process, the calculation scheme of the elastic system of the machine was developed. A simulation model for the study of dynamic processes that take place during the friction treatment of flat surfaces was built. This model gives possibility to determine the displacements and velocities of the machine table on which the part is fixed and the tool, and to determine their mutual displacement and also calculate the reaction of the machine table.
| 7. |
Gurey V. Topography of the strengthened cylindrical surface after frictional continuous treatment [Електронний ресурс] / V. Gurey // Ukrainian journal of mechanical engineering and materials science. - 2020. - Vol. 6, Num. 3-4. - С. 9-19. - Режим доступу: http://nbuv.gov.ua/UJRN/ujmems_2020_6_3-4_4 Abstract. Friction treatment refers to methods of surface strengthening (hardening) of the parts' working surfaces using highly concentrated energy sources. Concentrated energy flow is formed during high-speed friction of the tool on the treated surface in the area of their contact. A strengthened (reinforced) white layer with a nanocrystalline structure is formed in the surface layer of the treated surface. Friction treatment of cylindrical surfaces of samples made of steel 41Cr4 (hardening and low-temperature tempering) was made on a lathe, and the device for the autonomous drive of the strengthening tool was installed instead of a toolpost. The tool was used with a smooth working part and with transverse grooves on the working part. Experimental researches of the strengthened surfaces' topography were carried out on a profilometer "TALYScan 150" (Taylor Hobson Ltd, UK). The obtained data were processed in the software "Digital Surf MountainsLab Premium 8.2". After friction treatment by using the tool with transverse grooves on its working part on the treated surface more evenly distributed peaks than after friction treatment by using the tool with the smooth surface. Analysing the spectral density of the peak's distribution on the treated surfaces, it can be noted that after friction treatment by using the tool with transverse grooves, the area of the spectra is the lowest in comparison with friction treatment by using the tool with a smooth working part. When using the tool with cross grooves on its working part during frictional treatment allows to receive the best parameters of quality of the treatment surface in comparison with frictional treatment by the tool with a smooth working part. The parameters of the load-bearing capacity curve of the surface treated by the tool with transverse grooves on its working surface are better than after frictional treatment by the tool with a smooth working part. The treated surface by the tool with transverse grooves has a more favourable surface for wear, which was confirmed by research on wear resistance.
| 8. |
Hurey I. Effect of carbon content in steels on the formation of the strengthened layers during thermo-deformation treatment [Електронний ресурс] / I. Hurey, V. Gurey, T. Hurey, Y. Kholod, R. Hera // Ukrainian journal of mechanical engineering and materials science. - 2024. - Vol. 10, Num. 3. - С. 39-47. - Режим доступу: http://nbuv.gov.ua/UJRN/ujmems_2024_10_3_6
|
|
|